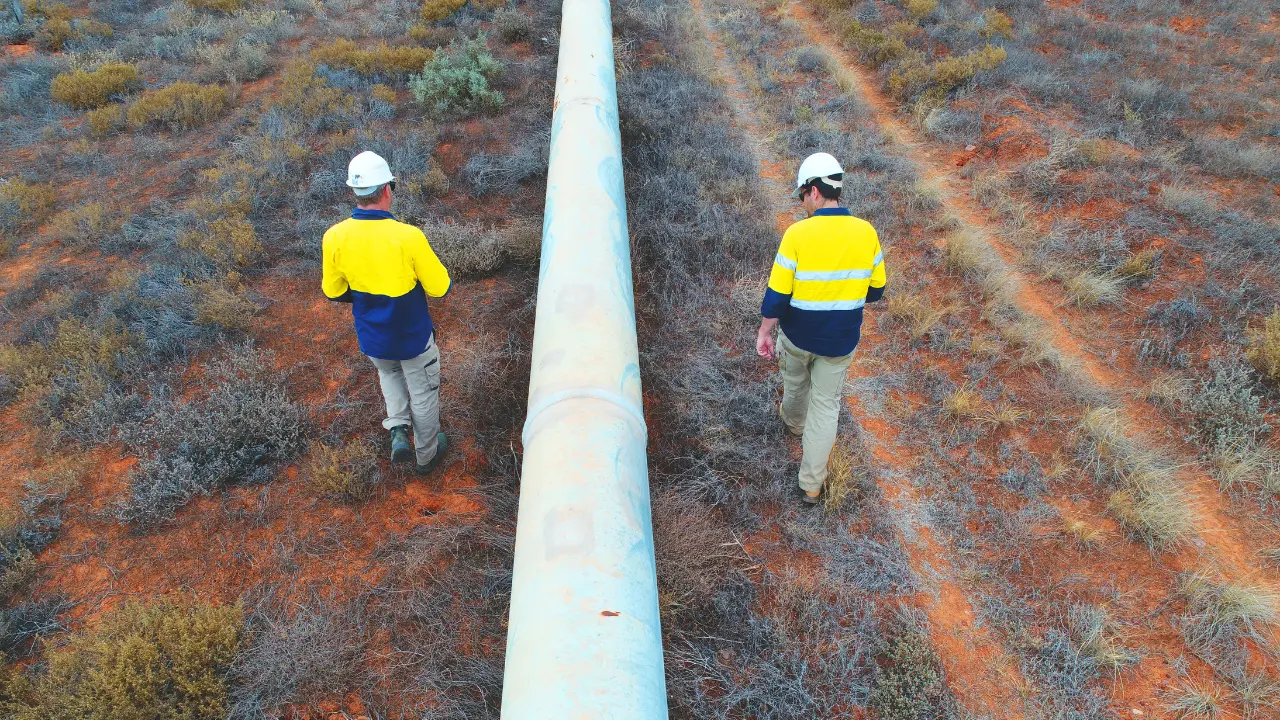
The energy industry evolves at a slow pace, with new industrial standards taking up to a decade to become widely accepted.
Utilities and O&G operators face significant barriers to change, from regulatory hurdles to risk management concerns.
This article explores the challenges of adopting new technologies, the lessons learned from past innovations, and how AI-powered satellite monitoring is shaping the next generation of energy industry standards.
Why Change Is Slow in the Utility Sector
10 years. That’s how long it takes to set a new industrial standard in the utility sector.
Energy companies are the backbone of our economy, and any major incident can result in millions of dollars in production losses, disrupt entire economies, and lead to fatalities, injuries, and devastating consequences for surrounding communities.
Every process, regulation, and standard exists to maintain the highest level of system integrity. In such a high-stakes environment, evolution is often seen as a risk.
Utilities oversee thousands—sometimes hundreds of thousands—of miles of infrastructure. It has taken them decades to harmonize their methods, ensuring system stability. As a result, new solutions are typically tested on only 1% to 5% of total assets before broader adoption. Scaling change introduces risks that utilities are hesitant to take.
Moreover, many of these companies operate as "frenemies"—technically competitors, yet rarely challenging each other’s territories, especially in centralized energy systems.
Some infrastructure projects take 10 to 15 years to develop, often requiring extensive local community and regulatory approvals.
With limited competition, utilities are caught in a paradox: no one wants to be the first to adopt a new solution, but no one wants to be the last either.
Adding to this challenge, new solutions often require changes in processes, skills, and IT infrastructure—a classic case of "change management." When combined with the industry’s inherent resistance to risk, even a demonstrably better solution can struggle to survive.
Overcoming Barriers: How Utility Companies Can Adopt New Solutions
Taking the above into consideration, is it impossible to implement new solutions for utility companies? The short answer is no.
However, success requires patience, resilience, and a long-term strategy.
Startups think in weeks and months; utilities operate on timelines of years—sometimes decades. The key is to identify the right expansion path and continuously demonstrate increasing value at each milestone.
There is a relatively "easy" playbook for adoption: if you can prove tangible savings—in the range of millions of euros—within just a few weeks, using the utility’s own data, while requiring minimal change management and leaving existing processes and standards intact, then you have a clear path forward.
However, for many other solutions, like SurfaceScout, LiveEO’s third-party interference detection system, the challenge is different. Initial pilot results are promising and outperform existing solutions, but not significantly enough for an O&G pipeline operator to immediately transition, given the scale, standardization, and change management challenges ahead.
Right now, the following ratio doesn’t work in our favor:
Short-term value / (Change management + Risks)
At least for now.
For structural reasons—mainly due to the number of sensors in orbit for the new space market—the drone market had a 10-year head start.
Looking at its evolution, we can extract valuable lessons on what it takes to establish a new industry standard.
Read also: The Biggest Challenges of Damage Prevention Managers
Lessons from the Drone Revolution: Transforming Wind Turbine Inspections
Wind turbines require annual or biannual inspections to detect damage affecting their integrity and performance—such as cracks, lightning strikes, erosion, or even fungal growth on the surface.
Traditionally, this was done by rope access technicians, who would climb along the blades, take photos, and later compile manual PDF reports—a process that took hours before results reached the customer.
Advantages of Rope Inspections
- High-resolution images with exceptional quality
- Direct human observation of the blade surface
- Potential for minor on-the-spot repairs
Downsides of Rope Inspections
- Lack of precision in defect localization
- Limited detection scope—if a technician missed something, it remained undetected
- Inconsistency—each operator followed a different approach
- No structured data—only unorganized PDFs stored locally
- Minimal traceability—making audits challenging
Despite these limitations, this method was deeply embedded in inspection plans, standards, and best practices. A legacy solution.
A few years later, robotic ground systems with telephoto lenses entered the scene, followed by drone-based inspection solutions. These alternatives reduced the need for human rope access but came with trade-offs:
- Image quality was lower than manual inspections, as cameras captured data from 10 to 100 meters away.
- Cost was lower but not drastically—around €600 per turbine, compared to €750 for rope technicians.
- Short-term value wasn’t a game-changer—while slightly more efficient, the shift wasn’t compelling enough to justify the change management and risk of adopting a new approach at full scale right away.
Once again, the key ratio Short-term value / (Change management + Risks) was not strong from the start.
After dozens of pilot projects, multiple expansion attempts by different companies, and thousands of inspected wind turbines, the long-term value of drone and software-based wind turbine inspections gradually became clear:
- Higher traceability – Every face of all three blades was captured with zero blind spots.
- A strong data backbone – Enabling better blade lifecycle management, improving design and manufacturing, and streamlining due diligence for blade health assessments.
- Software became the process – Manual, error-prone steps were eliminated through highly standardized and repeatable software-driven workflows.
- Lower inspection costs – At scale, the price per turbine inspection dropped to as low as €300 per turbine.
Short-term: Customers initially sought immediate OPEX reduction and better quality. However, they only achieved slight cost savings and at-best equal quality—not enough for rapid adoption.
Long-term: The entire industry benefited from a new, reproducible system that didn’t just cut OPEX but also improved CAPEX planning, risk monitoring, and overall asset management.
It took companies like Zeitview and Skyspecs nearly a decade to change the standard, integrating robots, software, and AI into a seamless inspection process. But now, in 2025, would anyone still consider sending a rope access technician to inspect a turbine blade?
The answer is clear.
O&G Pipeline Monitoring: Is Satellite Technology the Next Big Shift?
Oil & gas pipeline operators rely on a layered defense strategy for damage prevention—a Swiss cheese risk model—where multiple solutions work together to cover gaps in protection. These include:
- Vibration sensors
- Aerial inspections
- Drones
- Community involvement
- Ground signals, and more
Among these, aerial inspection remains a cornerstone, with some pipeline sections being monitored as often as daily in certain parts of the world.
Where does satellite monitoring stand in O&G pipeline monitoring?
- Sensor quality? Actually less good—satellite images have a 30 cm Ground Sample Distance (GSD), compared to 5 cm GSD for aerial monitoring at 300m altitude.
- Cost? Similar or slightly cheaper than aerial alternatives.
You see where this is going—our famous ratio is not good enough for immediate scale rollout and new standard establishment:
Short-term value / (Change management + Risks)
The question is now: how do we unlock the green value on the right of the schema chart?
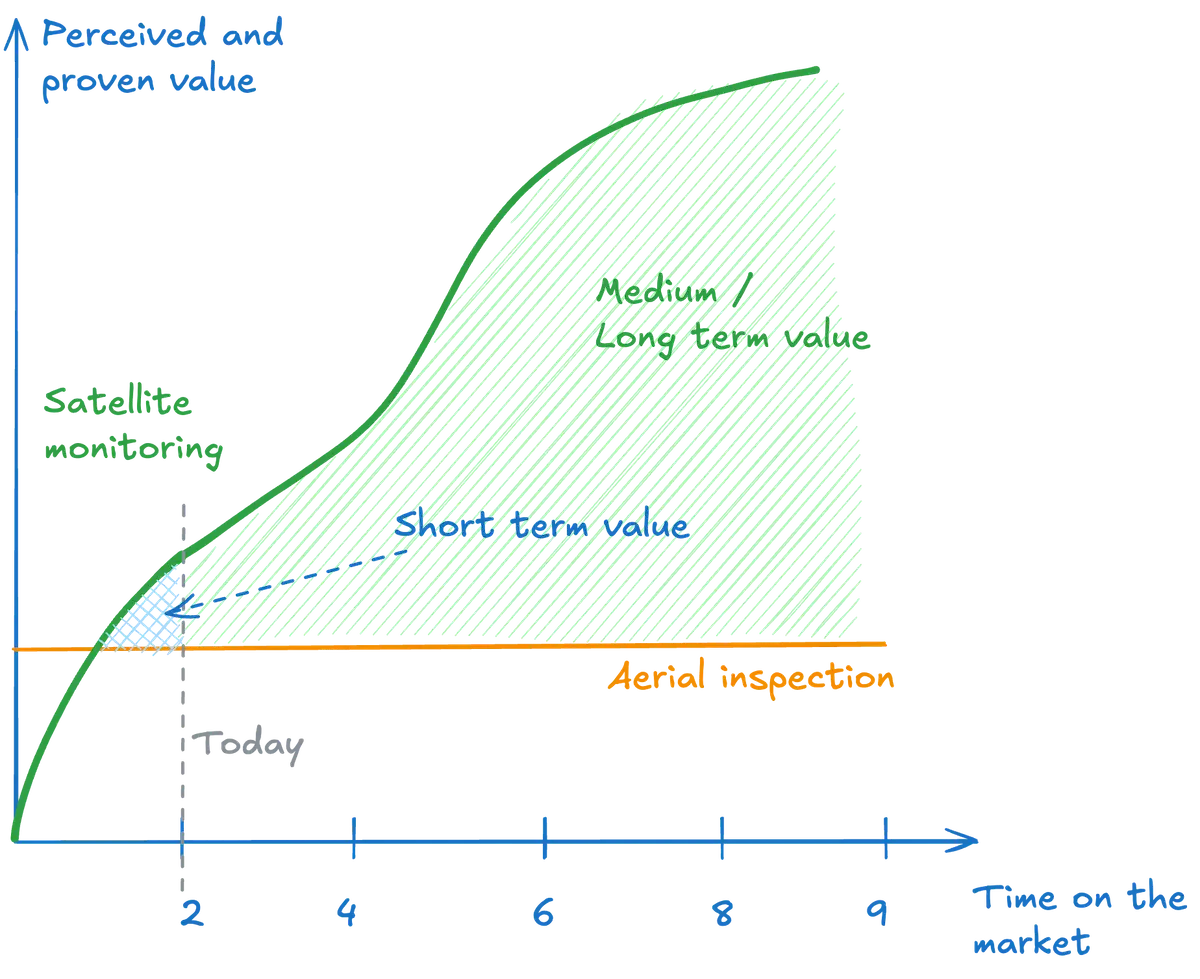
Scaling Satellite Monitoring: Unlocking Long-Term Value in Pipeline Safety, One Data Point at a Time
There are approximately 2 million kilometers of O&G pipelines worldwide. Assuming inspections occur every two weeks, and each 100 km segment generates 20 insights (our operational average), that translates to 10.4 million insights per year.
So far, we’ve inspected around 20,000 km, generating 4,000 insights—a small fraction of the global market. But even at this scale, we’ve already proven:
- Feature parity with aerial solutions–SurfaceScout detects the same risks as aerial inspections.
- Higher accuracy – We identify +73% more real risks (validated as relevant by users) than aerial methods.
This is promising, but—as we’ve seen—it takes 10 years to change an industry standard.
What’s Left to Do to Drive Adoption?
- Expand our early adopter network, strengthen the dataset, and refine key performance metrics to prove the medium-/long-term value
- Position ourselves as the new industry standard – Replace outdated systems with a proven and trusted alternative.
Read also: Five Key Reasons Third-Party Risk Monitoring Matters
The Current State vs Future State of Risk Mitigation in Energy
Current solutions aren’t perfect—but they are entrenched. Our mission isn’t just to introduce a better alternative; it’s to expose the hidden costs of maintaining the status quo and accelerate the transition.
Optimized Risk Mitigation
Current State: Aerial Inspections
- Human limitations – Inspectors can’t maintain 100% focus on the pipeline corridor while flying at 120km/h.
- Speed vs. accuracy trade-off – Rapid scanning increases the risk of missed issues.
- Weather & light conditions – Visibility is affected by atmospheric conditions.
- Lack of historical comparison – No systematic way to track changes over time.
Lower accuracy – 10 cm GSD images, often captured at an imprecise angle.
The result? Inconsistent monitoring and higher risk exposure.
Satellite + AI + Software Solution
- 100% pipeline coverage – No gaps, no blind spots.
- AI-powered detection – Consistent, exhaustive risk identification.
- Human-in-the-loop validation – Ensuring accuracy without increasing workload.
- +73% more real risks detected per inspection.
- Up to $5M in risk reduction per 1,000 km (validated by a major pipeline operator).
The outcome? A repeatable, scalable, and continuously improving risk mitigation process.
Eliminating Human-Based Processing Errors & Visualization Challenges
Current State: Aerial Inspection Reports
- Fragmented workflows – Reporting involves 5-10 manual steps (copy-pasting, visual checks, sorting).
- Outdated formats – Insights are delivered via emails, PDFs, and Excel sheets, stored in scattered locations.
- Lack of real-time visualization – No centralized dashboard for actionable decision-making.
Satellite + AI + Software Solution
- Seamless workflow – One continuous process from satellite data acquisition to insight generation.
- Fast decision-making – From space to your screen in just hours.
- Intelligent dashboard – Review, organize, and act on insights efficiently.
- Empowers subject matter experts – Reduces cognitive overload, allowing experts to focus on high-value tasks.
The outcome? A modern, user-friendly end-to-end risk management solution.
Building a Strong Data Backbone for Compliance & Traceability
Current State: Aerial Inspections & Compliance Risks
- In many jurisdictions, regulations operate on a “guilty until proven innocent” basis. No structured data system means there is no reliable way to confirm if a pipeline was fully inspected.
- Limited historical tracking – Past inspection records are difficult to access.
Risk of compliance failures – Lack of structured documentation complicates audits, legal investigations, and due diligence.
Satellite + AI + Software Solution
- Instant access to every inspection record – Fully searchable and timestamped.
- Complete historical tracking – Data is available in seconds, anywhere.
- Regulatory compliance made easy – Proof of due diligence at your fingertips.
The outcome? No gaps, no missing data—just full transparency and compliance.
Conclusion: Paving the Way for the Next Generation of Energy Standards
Bold, forward-thinking O&G pipeline operators will be the ones to pave the way for this new standard. In 3-5 years, what seems "new" today will become the obvious choice for risk mitigation. And in 10 years? No one will question it—this will simply be the way things are done.
Because this is what it takes to implement a new (better) standard in the energy sector.
Ready to future-proof your pipeline monitoring and risk mitigation strategy?
Book a consultation with Geoffrey today to explore how AI-powered satellite monitoring can transform your operations. Contact us now to schedule a strategy session and take the first step toward a smarter, safer, and more efficient energy future.
About The Author
Geoffrey Vancassel, Senior Product Manager, LiveEO
Geoffrey holds a Master of Science in Mechanical Engineering and has over a decade of experience in the remote sensing space. As the Co-Founder and CEO of Sterblue, Geoffrey developed software for drone inspections of critical assets like power grids and wind turbines. Additionally, Geoffrey co-founded Labelflow, an open-source software for building datasets to train machine learning models. Currently, Geoffrey serves as Senior Product Manager at LiveEO, leading SurfaceScout to enhance O&G pipeline safety by mitigating third-party interference risks using satellite data and AI.