Tesla wants to produce batteries as well as electric cars in Grünheide. But it is unclear when the battery plant will start up. Competing battery manufacturers, meanwhile, could overtake Tesla. They are about to start production, as exclusive satellite images show.
“Economy from above” is a collaboration between WirtschaftsWoche and LiveEO. This is a translation of the original article written in German by “Martin Seiwert“. Access the original article here.
Electric cars are selling better than even the most optimistic forecasts had predicted. Accordingly, demand for e-car batteries is exploding. Most of the battery cells that German automakers install in their cars in this country come from China, South Korea and Japan. But in the long run, importing the cells is too costly and CO2-intensive. That’s why carmakers and battery companies are currently building cell factories across Europe.
A factory that is reportedly almost ready is located in Grünheide: Tesla wants to manufacture batteries as well as e-cars in Brandenburg and thus supply its entire European production.
But the Tesla battery plant is still at a standstill. It is not known when it will be possible to start production there. Construction sites of other European battery manufacturers are further along – production is already underway there or there are official production starts before the end of the year. Exclusive satellite images from LiveEO show the real state of play.
The Volkswagen Group is planning the most massive battery investments of all European manufacturers. Europe’s largest carmaker wants to manufacture largely all the batteries it needs, including the battery cells, itself in the future. In Salzgitter, Lower Saxony, the Group laid the foundation stone for its first battery factory at the beginning of July. Five more are to follow in Europe. Production is scheduled to start in Salzgitter in 2025. “In the future, we will take all relevant fields into our own hands and thus secure a strategic competitive advantage,” says Thomas Schmall, VW’s head of technology responsible for the battery factories.
.jpg)
.jpg)
.jpg)
.jpg)
.jpg)
As yet, all that can be seen in Salzgitter is a cleared site and initial construction work next to the VW engine plant, which has been in operation for decades. Once battery production is up and running, it is expected to provide 5,000 jobs. In Europe, Volkswagen plans to employ up to 20,000 people in battery production. VW’s global battery business is to be managed from Salzgitter under the umbrella of the newly founded Group subsidiary PowerCo. It will then be responsible for the entire value chain from battery raw materials to production and recycling. There will also be a battery research center in Salzgitter. According to VW forecasts, PowerCo is expected to generate sales of over 20 billion euros in 2030.
The work of the Chinese battery manufacturer CATL in Thuringia is not as large as VW’s plans, but it is much more advanced. Hardly noticed by the general public, CATL – short for Contemporary Amperex Technology – has risen to become the largest battery cell manufacturer in the world. The company is currently in talks with almost every carmaker in the world about larger battery cell supplies. Probably fortunately for the German auto industry, the company announced the opening of an electric car battery cell factory south of Erfurt in late 2018.
Construction has been underway there since October 2019. After several delays, including due to the corona pandemic, series production is scheduled to start in the second half of 2022. 1500 employees are to produce batteries for 120,000 e-cars annually in the first expansion stage. According to Matthias Zentgraf, head of CATL Europe, they will go to the VW Group, BMW and Daimler.
Daimler, unlike VW or BMW, for instance, already has its own battery factory in Germany, it is often said. In fact, the Swabians obtain their batteries from the Daimler subsidiary Accumotive at the Kamenz site in Saxony, among others. However, the actual technology carriers, the battery cells, are not manufactured there. Accumotive does what BMW or VW also do: The company assembles Asian battery cells into complete car batteries.
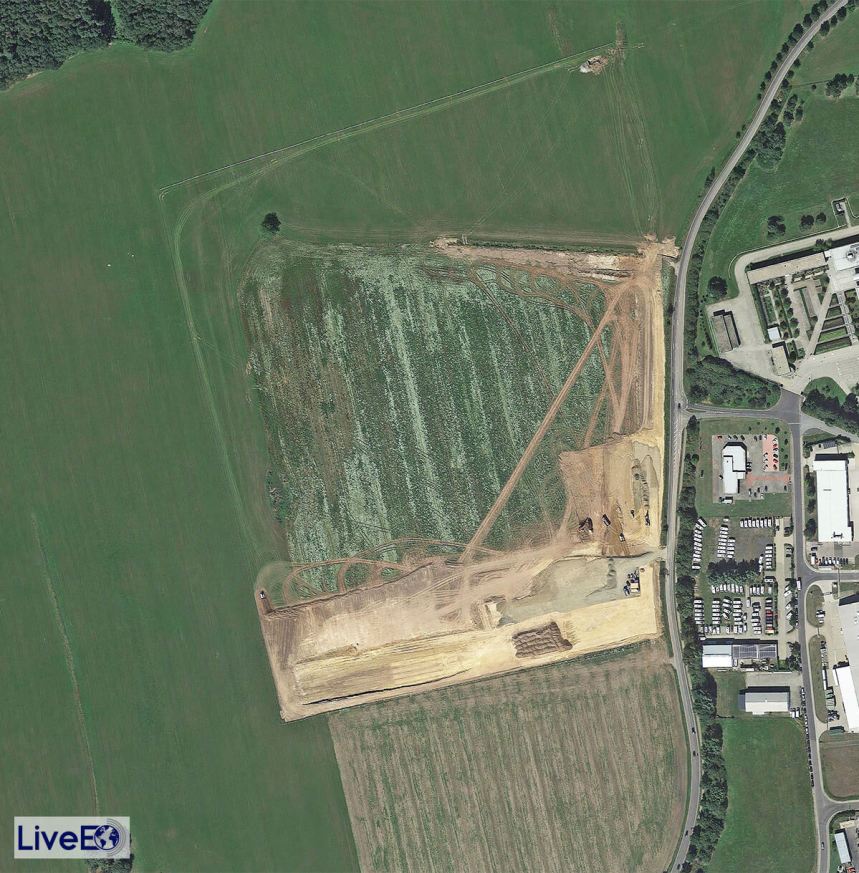
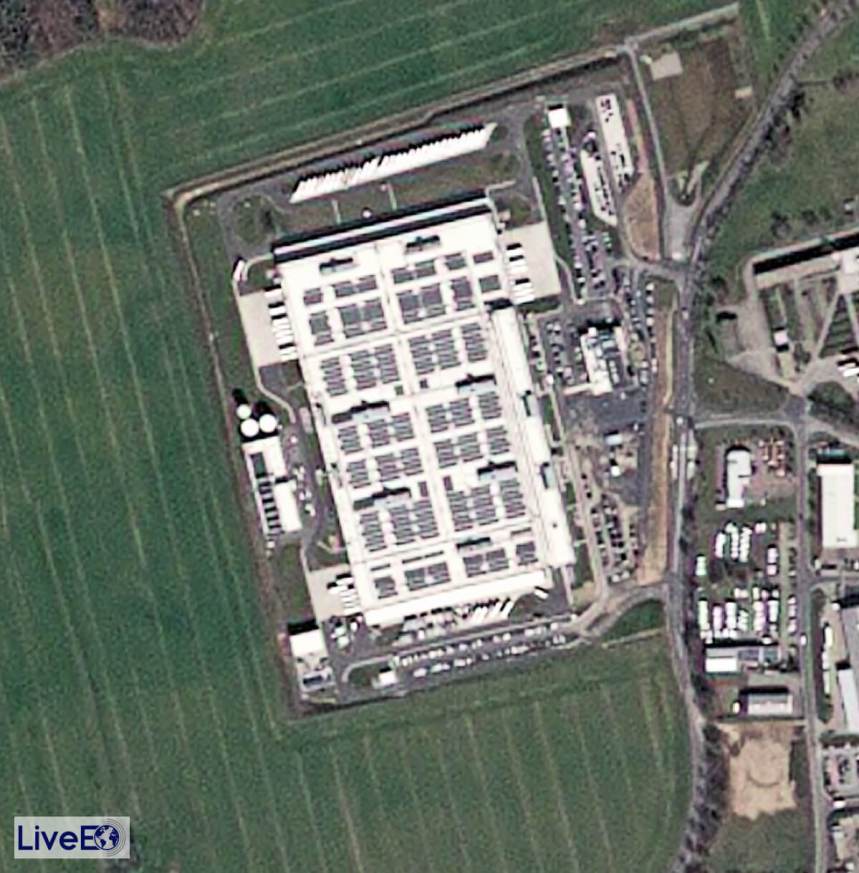
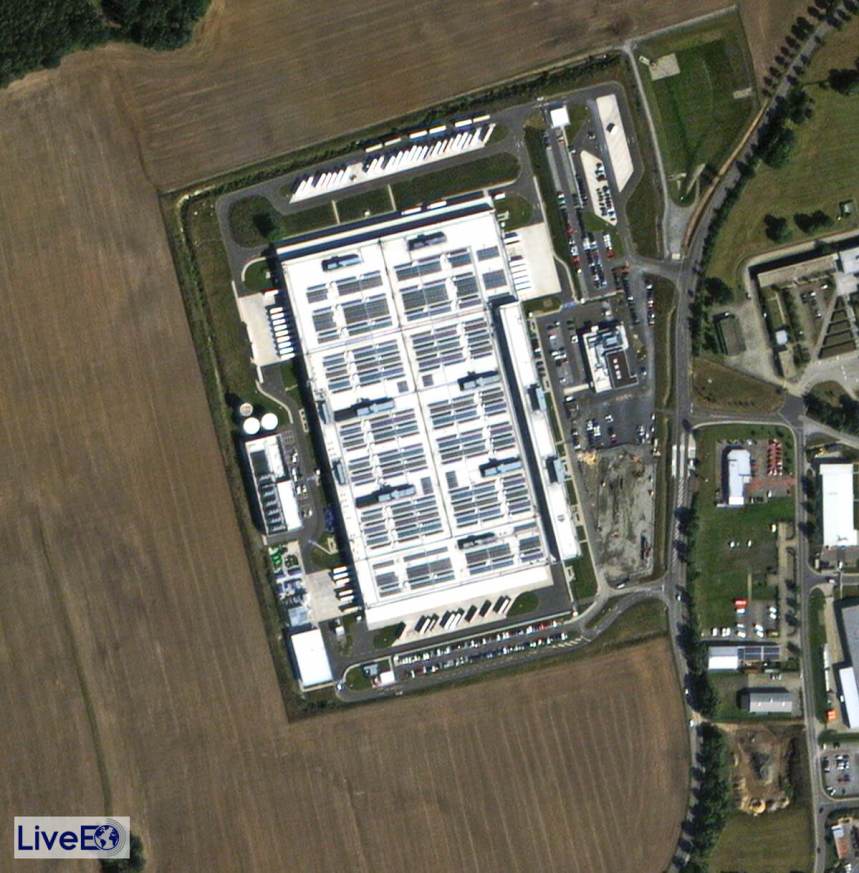
This is also an important area of expertise, because the connection of hundreds of individual cells per car is not trivial and can be decisive for the performance and safety of e-vehicles. Nevertheless, the assembly of battery cells is not a battery cell factory like those operated by Chinese or Korean market leaders or the U.S. company Tesla.
Accumotive has been building traction batteries for hybrid and electric vehicles from Mercedes-Benz and Smart as well as for commercial vehicles with the star at the Kamenz site since 2012. The site has two battery factories. The second factory was added in 2018 and is designed to produce in a CO2-neutral manner. A combined heat and power plant, a photovoltaic system and geothermal energy supply the factory with energy.
The approximately 1,300 employees there manufacture, among other things, drive batteries for the EQ models. The second factory increased the production and logistics area to a total of around 80,000 square meters. Since the start of production, Accumotive has built batteries for well over one million vehicles in Kamenz.
In the long term, however, Daimler does not intend to be content with assembling battery cells, but – like the Volkswagen Group, for example – wants to get involved in the production of battery cells: In 2021, Daimler announced that it would take a 33 percent stake in ACC, a cell consortium of the car manufacturer Stellantis (brands: Opel, Peugeot, Citroën, Fiat, Chrysler, Alfa Romeo) and the French oil company TotalEnergies. ACC intends to develop and manufacture high-performance battery cells in Europe. This should reduce dependence on Asian cell manufacturers. Daimler CEO Ola Källenius said of the venture, “We are making a contribution to ensuring that Europe remains a center of the automotive industry.”
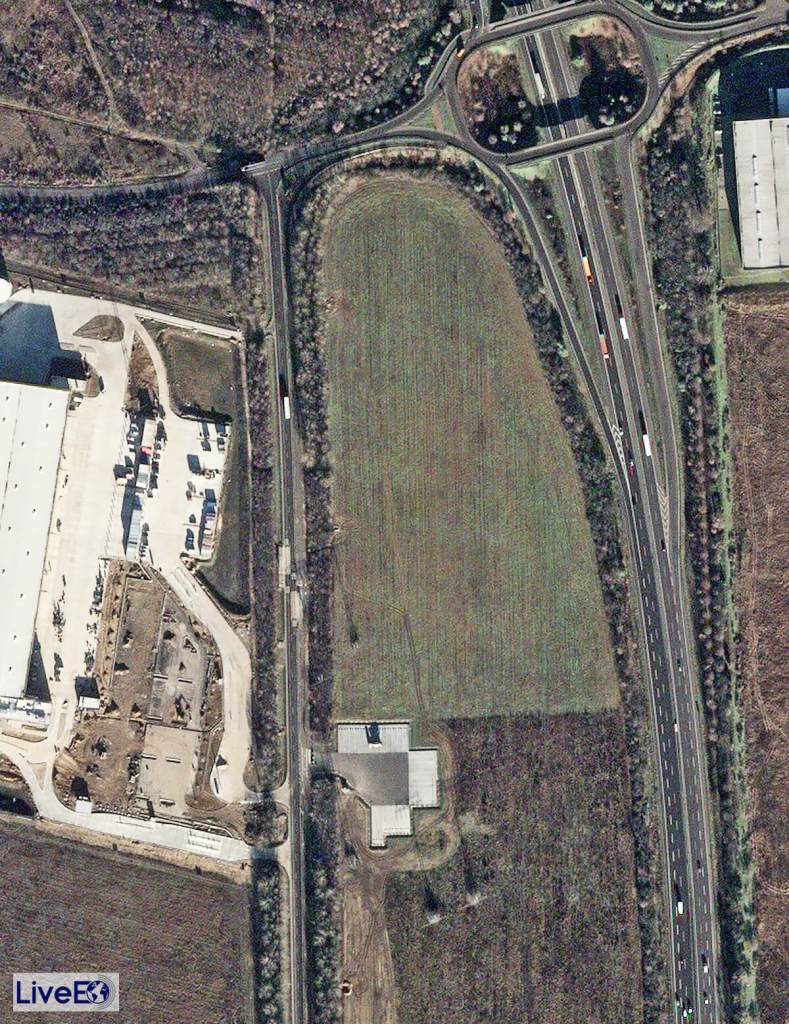
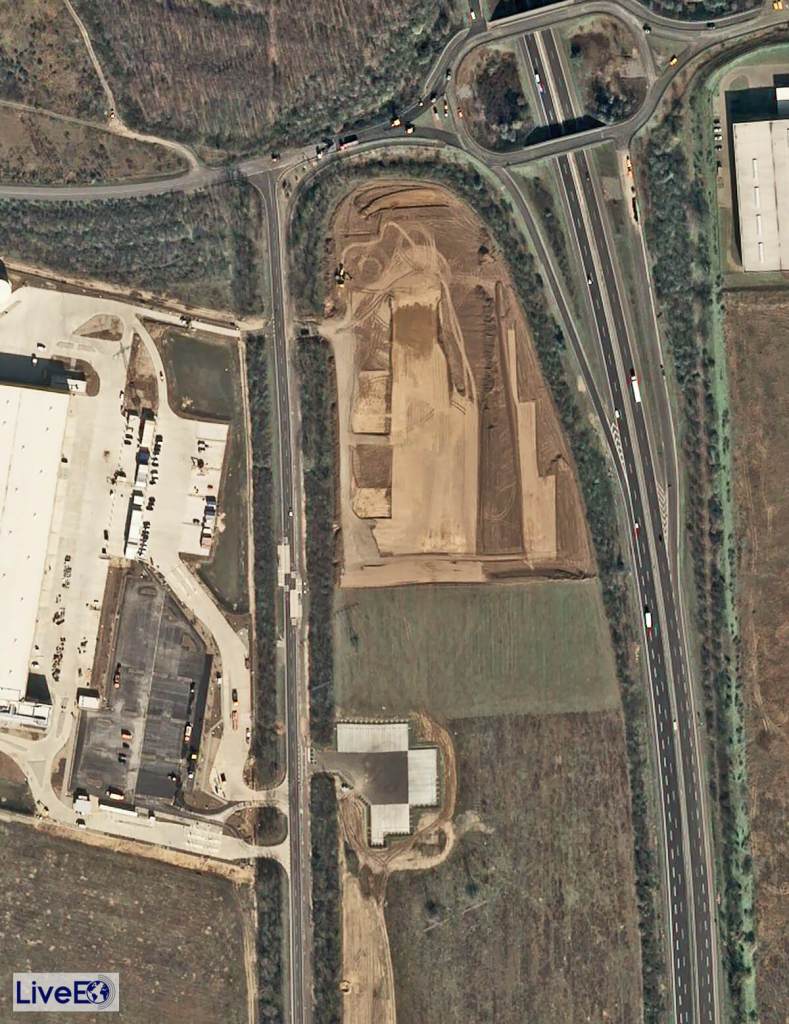
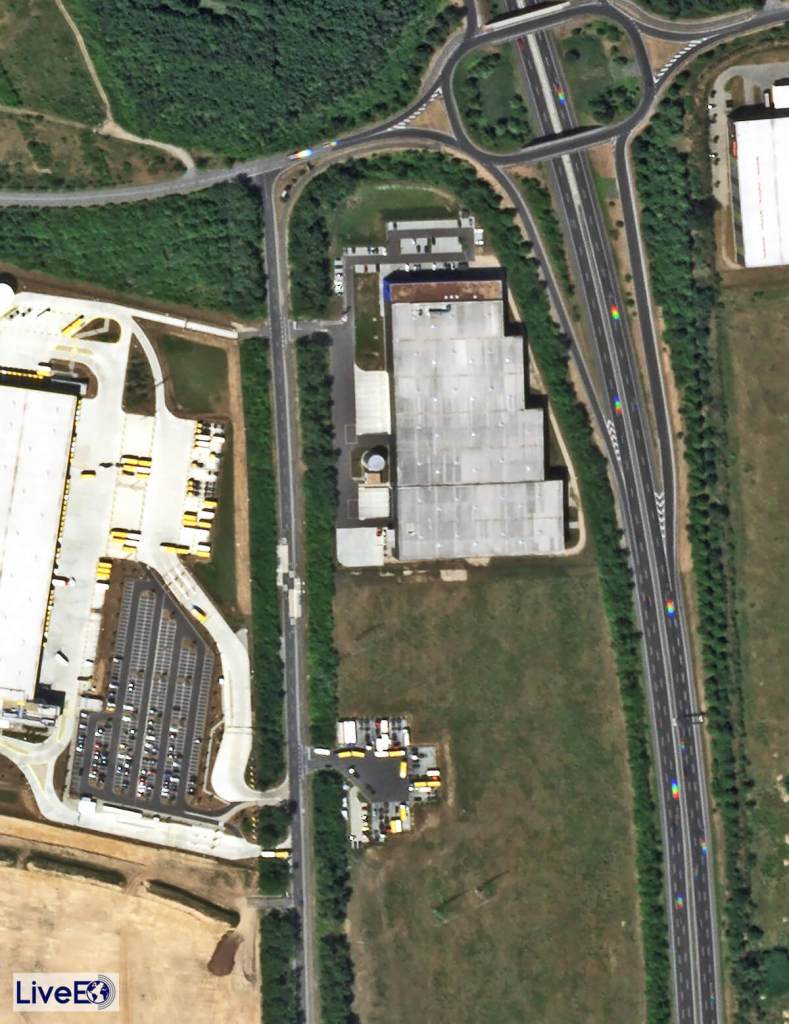
Two years ago, the U.S. company Microvast celebrated its topping-out ceremony in Ludwigsfelde, Brandenburg: within a few months, a white factory building had been erected there. The company not only wants to produce here: At the beginning of 2021, Microvast also moved its European headquarters from Frankfurt to Ludwigsfelde. For more than a year now, the company has been building special battery systems in Brandenburg for vans and trucks as well as for sports or off-road vehicles. They are made from battery cells that Microvast sources from China. This summer, it also plans to produce cells at a new plant in Clarksville in the US state of Tennessee.
Ludwigsfelde will soon also be home to a new technology. Microvast recently presented two new lithium-ion cells that are said to be particularly suitable for special and commercial vehicles. The cells can be charged to 80 percent in just 16 minutes and are said to have a long service life. Microvast is planning mass production of the cells, which will then also be processed into complete batteries in Ludwigsfelde, for next year.
The German automakers are less interested in a German counterweight to Asian battery cell dominance than in a European one. There must be production capacities and in-house know-how in Europe, according to the view of VW & Co, if they are not to become completely dependent on China, South Korea and Japan.
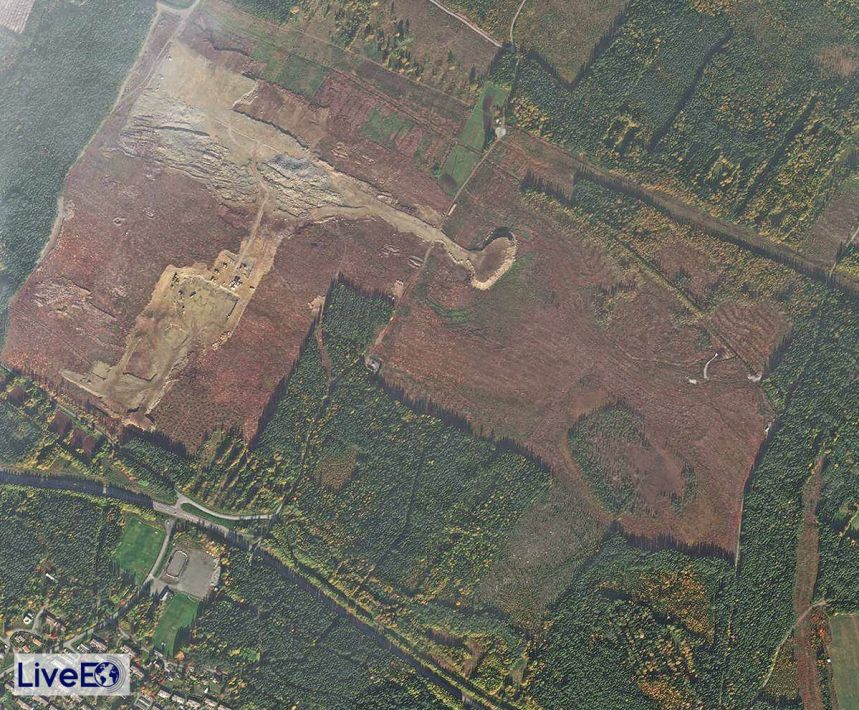
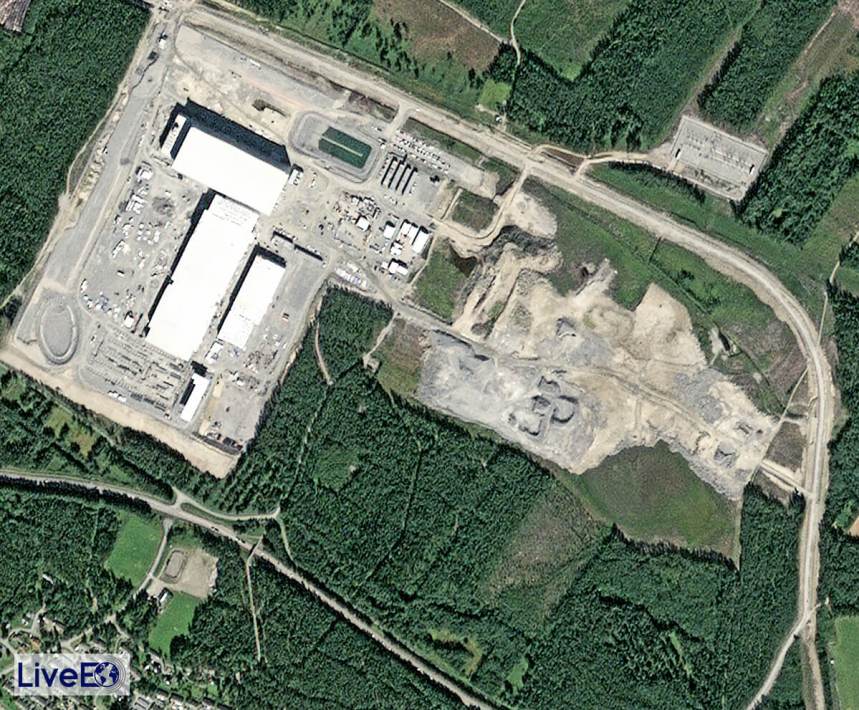
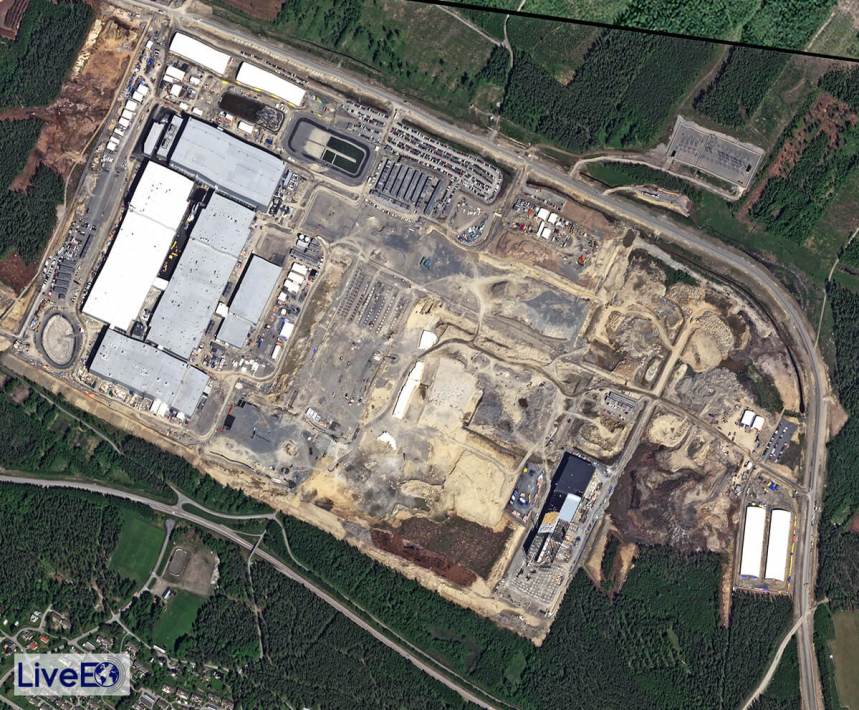
The young Swedish battery manufacturer Northvolt comes just at the right time for the Germans. Volkswagen and BMW have already agreed to cooperate with Northvolt. The company has secured a total of around eight billion euros from investors for the massive expansion of production. Among other things, Northvolt used the money to build the main factory in Skellefteå in northern Sweden, which can be seen in the pictures and where production began at the end of 2021. The factory has been delivering cells to automakers since this spring. Northvolt has orders worth more than 50 billion euros on its books, including from the VW Group, BMW, Volvo Cars and Scania.
Recently, Northvolt announced the signing of a $1.1 billion convertible bond. The company intends to use the fresh capital to accelerate battery cell production in Europe. Among other investors, the VW Group participated in the capital increase. Northvolt not only wants to produce the cells, but also recycle them. The goal is for half of the company’s raw material requirements to come from recycled batteries as early as 2030. Peter Carlsson, co-founder and CEO of Northvolt, promises: “We will continue to work hard to deliver on our promise to build the greenest battery in the world.”
In addition to the Northvolt Ett Gigafactory in Skellefteå, the company is also building a gigafactory in a joint venture with Volvo Cars in Gothenburg and another, called Northvolt Drei, in Heide in Schleswig-Holstein. It is also building a cathode factory in Borlänge, Sweden. Northvolt was only founded in 2016 – by two former Tesla managers.